Galvanized Iron Wire
Metal and corrosion will always find their way to each other. One of the best preventions against this process is the galvanizing process. Galvanized items or objects have a zinc coating on them which prevents corrosion of the metal. Without this protection, there is no way for oxidation and corrosion to be imminent.
Galvanized Iron or GI wires is a special kind of iron wire. These wires are special due to their method of preparation and their constituencies. These wires are made by immersing them in zinc. A layer of zinc acts as a resistant coat to moisture which prevents the wires from rust and corrosion. There are two ways in which this is done:
- Hot-dip galvanizing
- Electroplating Galvanized Iron wire
Hot Dip Galvanizing
Hot-dip galvanizing works for both external and internal surfaces and have the ability to self-repair when damaged. This galvanizing method involves dipping base metal into the molten zinc. The hot-dip process involves three major steps.
- Surface Preparation
This step involves the proper cleaning of the metal before the hot bath because an unclean surface will fail to hold the zinc coating, thereby failing to protect the steel for expected years. Zinc will not react unless the metal is clean because it reacts with the metal surface and not the impurities. This process includes sub-steps, including degreasing, pickling, and fluxing.
- Galvanizing
The next process involves the clean steel dipped into the molten zinc which has 98% pure zinc, molten at a minimum of 435°C. The zinc will react with the iron available in steel and form a series of layers which is protective against corrosion.
- Inspection
The inspection process is for checking whether the coating is good in quality, thickness, and in adhering to ASTM standards.
Hot Dip Galvanization Advantages
- Higher durability and longer life time
- Economical
- Quick process
- Can cover complex shapes of objects
- Environmentally sustainable process
Cold Dip Galvanizing
Cold dip galvanizing involves zinc coating through zinc-rich paints, which can be done with the help of brushes, spray guns, rollers, electro-galvanizing, etc. The paint contains a binding compound that helps in the mechanical bonding of the paint and steel to create a proper protection layer against corrosion.
Cold Dip Process
The cold dip process is generally a painting process and doesn’t require as much preparation as hot-dip galvanization. But the starting of the preparation is similar- the metal base needs to be clean and dry. Initially, wire brushes can be used for rust removal, but eventually, grease, dirt, or other organic compounds must be removed as well. After the surface is clean, zinc coatings will be applied as needed.
Cold Dip Advantages
- You can have control over rust-thickness
- Minimal preparation of the object
- Offers weldability
- Can be retouched with extra coating as and when needed
Thickness
- Hot Dip: Hot-dip coating is a bit thicker and can be 30-80 um. This is why it offers a long service life.
- Cold Dip: Cold dip galvanizing has a smooth, uniform, and thinner coating (up to 35 um) as compared to hot-dip coating.
Our galvanized wire has good toughness and elasticity. The amount of zinc can reach up to 100 grams per square meter. It has the characteristics of thick galvanized layer and strong corrosion resistance.
- The wire diameter ranges from 0.3mm to 6mm.
- The coil weight can be from 15 to 800 kg.
- The tensile strength varies between 300-2200 MPA based on the size and base material which is going to be galvanized.
There are various sectors that immensely depend upon the use of Galvanized Iron wires. These are as follows:
- For fencing
- For farming
- For poultry
The varied reasons behind the use of Galvanized Iron wires are as follows:
- It Provides Strong Protection:
The sturdy nature of these wires aid in providing strong protection wherever they are applied. For example, in farms, they prevent stray animals from getting into the farm thereby keeping the plants safe.
- It is Easily Accessible:
Due to their widespread availability, these wires are easily found at any hardware store. This further accelerates their use in daily life.
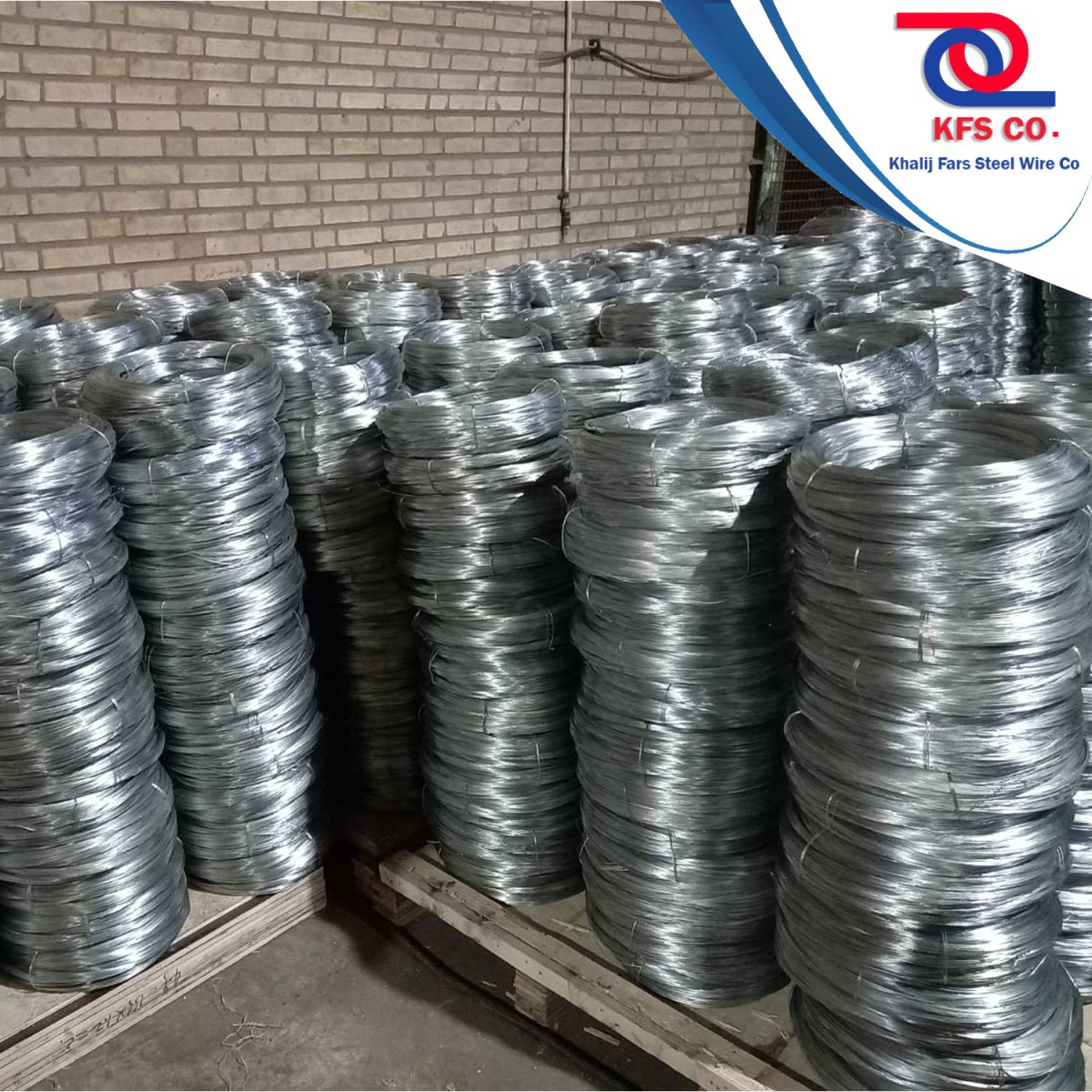
- It is Highly Versatile:
Despite being sturdy, these wires are immensely versatile, which means that they can be used for multiple purposes. These include fencing for fields and houses.
- It is Cost-Effective:
These wires are sturdy, resilient, and comparatively cheaper than other kinds of widely available wires. This effectively increases their overall demand.
- It Can be Customized:
Galvanized Iron wires can be easily personalized according to requirements. For example, the galvanized wire you use for making cages for tomatoes and creepers can also be used to make mesh for poultry.
- It is Quick to Install:
These zinc-coated, rust-free wires are immensely easy to use. You can simply cut them with a wire cutter and use them for your specific requirement without any added worries.
- It Gives You a Better View of Your Property:
Since these wires are moldable according to your specific use, you can shape them to keep an eye on your property as well. For example, when placed around your farm, they’ll act as a see-through alongside protecting your plants.
- It Adds Value to Your Property:
All properties that are surrounded by galvanized iron wires are considered better. This is mainly due to added safety and efficacy.
Galvanized wires are immensely handy and easy to use. This makes them one of the most sought-after hardware in every household.